You are here :
Home Sudamdih Colliery on 4.10.1976
|
Last Updated:: 01/06/2015
Sudamdih Colliery on 4.10.1976
Sudamdih Colliery
Date of the Accident |
- 4.10.1976 |
Number of persons killed |
- 43 |
Owner |
- Bharat Coking Coal Ltd. |
Place |
- Jharia Coalfield |
A firedamp explosion occurred in the 400 m horizon workings of XV seam on 4.10.1976 at about 0840 hrs. The explosion occurred between the second and third rises. There were four closed holidays (30.9.1976, 1.10.1976, 2.10.1976 and 3.10.1976) on account of Durga Puja immediately preceding the accident.
The XV seam is 6 to 7 m thick and has igneous intrusions which have burnt the coal to “jhama” at places. Gas survey conducted in May 1973 had shown a gas emission of upto 8 m3/min and it was classified as a gassy seam of the third degree. The depth of the seam in the area of the accident was about 400 m. The dip of the seam varied from about 27° to 60°. The 400 m horizon workings are entirely below the river Damodar.
Method of work
The seams at Sudamdih have been opened up on the horizon system of mining. Three horizons, namely, 200m, 300m and 400m, have been developed to work XV, XIVA, XI/XII and IX/X seams. Rises at 100 m intervals have been driven from the lower to the upper horizon to form blocks of coal for subsequent extraction. All roadways are driven by blasting off-the-solid. The pattern of development is shown in Fig.1.
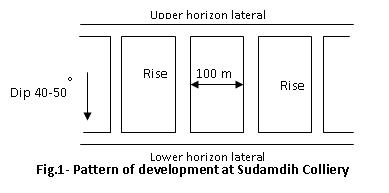
In the XV seam, companion galleries to the main lateral gallery are driven off these rises leaving coal blocks of 25 m to 30 m. The companion galleries are shown in Fig.-2.
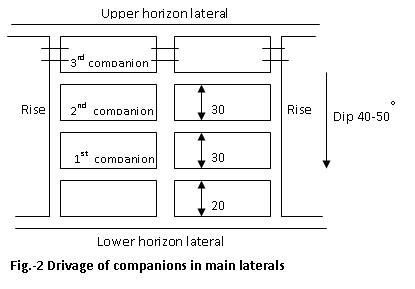
Room rises at 10m intervals are driven from the lowest companion to the next higher companion.
Thus in each wing of the block, 10 rooms can be formed. The cross-section of these room rises is 3 m x 2 m. Each room is widened to a total width of 7 m and heightened upto the main roof which is normally 7 m from the floor. Extraction of the room is carried out from dip to rise with solid blasting. This method of extraction is called the “Komora” method. The rooms, when regular extraction of coal commences, are referred to as “Komoras “. Complete extraction of a “Komora” normally takes 15 days. After extraction, the “Komoras” are stowed with sand.
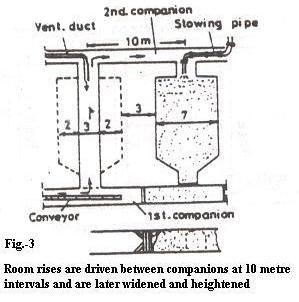
Conditions prior to the accident
The last working shift before the accident was the third shift of 29.9.1976. Normal mining operations were suspended during the holidays. Many of the officers, including the General Manager, were on leave during the Puja period. A roster duty chart was prepared according to which one Assistant Manager or Under Manager or JET, one Overman or Mining Sirdar and one Electrician or Electrical Helper would be on duty in each shift during the holidays. However, due to various reasons, during the entire holiday period, only one officer (an Under Manager) visited the XV seam workings in the third shift of 1.10.1976. No officer went underground on 2nd and 3rd October. On 3rd October the Under Manager and Mining Sirdar who were on roster duty in the second shift left the mine at the end of the shift without waiting for their respective relief. In the third shift, neither the Under Manager nor the Mining Sirdar came for their roster duty. Both pleaded illness in their evidence. The mine Time-keeper also failed in his duty to inform senior officers that no one had turned up for roster work in that shift.
The result of these lapses was that no check on the auxiliary fans was made by anyone at least during the last shift before the mine reopened on the morning of 4th October. It was subsequently found out that out of the six auxiliary fans in the affected area; at least three did not work at least in the third shift on 3.10.1976. Stoppage of auxiliary fans had caused accumulation of inflammable gas in a number of places. On 4th morning, either the working places were not checked for gas before employing the workers or, even if they were checked and gas was detected, persons were not evacuated before starting the fans. An explosive mixture was formed and the explosion occurred within a few minutes of the starting of the fans.
Factors leading to the explosion
-
(a) Gas accumulation
Prior to the accident, the following 5 blind headings were under drivage:
400m lateral |
along the strike line of the seam |
3rd companion |
-do- |
4th rise |
towards the rise of the seam |
3rd rise |
-do- |
6th room rise |
-do- |
During the course of the inquiry, a study was undertaken on gas emission in the different drivages. Taking into account the capacities of the auxiliary fans in the different drivages, it was observed that gas accumulations from these drivages, could be cleared in the time shown against each:-
400m lateral |
182 seconds |
4th rise |
182 seconds |
3rd rise |
144 seconds |
6th room rise |
Within a few seconds |
3rd companion |
Did not indicate gas accumulation except in small pockets in roof cavities |
The likely places of gas accumulations were identified as: 400 m lateral, 4th rise, 3rd rise, 6th room-rise and 3rd companion. The faces of 3rd rise and 3rd companion had been blasted in the last shift of 29.9.1976 before closure for Puja holidays. Fresh exposure of coal and broken coal would have contributed to some increase in gas emission in these places. There was also a possibility of some gas accumulation in the three “Komoras” due to the construction of barricades for stowing and the 4th , 5th , 6th , 7th and 8th room-rise due to inadequate air flow.
The Court thus came to the conclusion that the explosion occurred in the zone between the 1st and 2nd companion bounded by the 2nd and 3rd rises.
-
(b) Source of ignition
It is unfortunate that the source of ignition could not be pin-pointed. No explosives were taken underground and locomotives did not travel in the affected area on the day of the accident. No flame safety lamp was taken to 400m horizon. Contrabands like matches or other sources of lighting were not detected underground. Men were thoroughly checked for contrabands before they entered the cage. However, nine “agarbatti” sticks were reported to have been found in the 1st companion gallery by the captain of rescue team No.8. But the statements of the team members differed from that of the captain in a number of details. The Management’s representative stated that “agarbattis” being the source of ignition was not possible. Some Trade Union representatives felt that the “agarbattis” were planted. DGMS in their statement said that the captain’s statement did not appear to be convincing. The Court concluded that the “agarbattis” were definitely not in the 1st companion at the time of the accident and were ruled out as a possible source of ignition.
There was no evidence of any sparking or flashing in any of the damaged cap lamps recovered from the accident site. After all the electrical equipments in the affected area were examined by experts, the Court ruled out electrical sparking as a source of ignition. Sparks arising out of compressed air equipment were also ruled out because the two loading machines, which were the only compressed air operated equipment in the area, were not operated. Frictional sparking produced in auxiliary fans due to rubbing of blades against the liner or guide vanes was also ruled out firstly because in none of the fans, blades were found rubbing against the guide vanes and secondly, CMRS tests showed that rubbing of blades against the aluminum liner did not produce an incendive spark.
The Management’s representative had suggested that the ignition was probably caused by a spark produced by a piece of stone from the sill in the 2nd companion falling on the conveyor structure. DGMS suggested the possibility of fall of roof stone from the sill in 6th room-rise. The spark could also be produced by rubbing of a metallic part of the conveyor against a stone. One witness had heard a casualty saying that, “he was at the loading point at the time of the blast. Some machine was started and immediately thereafter came the big bang”. After considering all the evidence, the Court was of the opinion that in all probability the ignition was caused due to rubbing of stone against the metallic parts of the conveyor when it was started.
Observations and recommendations of the Court
(Main points summarised)
- Some officers and supervisors of the mine showed good leadership and dedication to their duty towards their men. Risking their own lives, they went into the affected area immediately after the explosion, even without a methanometer or flame safety lamp, and saved a number of lives. Their conduct and behaviour deserve the highest praise.
- Proper arrangement should be made for supervision of the mine during holidays. At least in gassy seams of the third degree, all working faces should be inspected by an officer in each shift even on holiday. On the first working shift after a holiday, an officer should be deputed to check for gas in all parts of the mine before workers are allowed in.
- CMR-44(8) requires that a Sirdar shall not leave his district unless relieved by a successor. This provision regarding handing over charge by the Sirdars in the district (i.e. belowground) should be strictly enforced. Overmen should also be enjoined to wait until they are relieved. During rest days and holidays, persons on roster duty should also be required to go only after handing over charge to their successors.
- CMR-186 lays down that “no machinery shall be operated otherwise than by or under the constant supervision of a competent person”. Quite often auxiliary fans are operated by miners. Competent persons should be authorized to handle these fans. They must ensure that the fans are started in proper sequence.
An environmental survey should be conducted before the capacity and location of auxiliary fans are decided upon. The survey should take into account the possible ill effects of running an auxiliary fan on the neighbouring working places as well as the places being ventilated by the auxiliary fan. Such surveys should be carried out periodically even after installation of the fan as there can be variation in gas emission and air circulation.
- There were not enough methanometers and flame safety lamps in working order to meet the daily requirements of overmen and mining sirdars. This situation needs to be corrected. Even though methanometers are now in common use for detection of methane, the only equipment mentioned in the CMR is the flame safety lamp. The CMR should be suitably amended to make the use of methanometers lawful.
On the day of the accident, no flame safety lamp was taken to the 400m horizon by any of the officials and it is doubtful if tests for the presence of inflammable gas were made with methanometers in all the relevant areas. It is recommended that additional precautions for Degree III mines should be taken by installing an automatic multi-point methane recorder. Additionally, automatic methane alarms should be placed at all faces where gas is likely to accumulate.
- The rescue work in 300 m horizon was done promptly and completed by about 12 noon, yet there was too much delay in dealing with 400 m horizon where the accident had actually occurred. The Control Room was made aware of the serious situation in 400 m horizon but it dithered and did not issue any direction for work to start in 400 m horizon. The whole thing was managed so badly that the first rescue team started work in 400 m horizon only at 1600 hrs, i.e. more than 7 hours after the accident.
There are no clear instructions as to who should take control of rescue and recovery operations in an emergency. In this case no one seems to have performed this duty effectively. In the view of the Court this responsibility should be given to a committee consisting of a senior officer of the mine (who has detailed knowledge of the mine), a representative each from DGMS, Rescue Station and the recognised Trade Union. This committee should take decisions and direct operations from the Control Room.
- In each mine there should be a standing order with regard to the action to be taken when there is an accident.
Also there should be definite emergency plans for every mine and rehearsals should be undertaken periodically for evacuation, rescue operations, etc.