STANDARDS FOR TREATMENT AND DISPOSAL OF BIO-MEDICAL WASTES
BIO- MEDICAL WASTE (MANAGEMENT AND HANDLING) (SECOND AMENDMENT) RULES, 1998
I.STANDARDS FOR INCINERATORS :
All incinerators shall meet the following operating and emission standards
(a) Operating Standards
- Combustion efficiency (CE) shall be at least 99.00%.
- The Combustion efficiency is computed as follows:
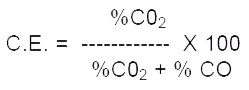
- The temperature of the primary chamber shall be 800 ± 50 deg. C°.
- The secondary chamber gas residence time shall be at least I (one) second at 1050 ± 50 C°, with minimum 3% Oxygen in the stack gas.
(b) Emission Standards
Parameters
- Particulate matter
- Nitrogen Oxides
- HCI
- Minimum stack height shall be 30 metres above ground
- Volatile organic compounds in ash shall not be more than 0.01%
Concentration mg/Nm3 at (12% CO2 correction)
Note: -
- Suitably designed pollution control devices should be installed/retrofitted with the incinerator to achieve the above emission limits, if necessary.
- Wastes to be incinerated shall not be chemically treated with any chlorinated disinfectants.
- Chlorinated plastics shall not be incinerated.
- Toxic metals in incineration ash shall be limited within the regulatory quantities as defined under the Hazardous Waste (Management and Handling Rules,) 1989.
- Only low sulphur fuel like L.D.0dLS.H.S.1Diesel shall be used as fuel in the incineration.
II.STANDARDS FOR WASTE AUTOCLAVING :
The autoclave should be dedicated for the purposes of disinfecting and treating bio-medical waste,
- When operating a gravity flow autoclave, medical waste shall be subjected to :
- a temperature of not less than 121 C° and pressure of 15 pounds per square inch (psi) for an autoclave residence time of not less than 60 minutes; or
- a temperature of not less than 135 C° and a pressure of 31 psi for an autoclave residence time of not less than 45 minutes; or
- a temperature of not less than 149 C° and a pressure of 52 psi for an autoclave residence time of not less than 30 minutes.
- When operating a vacuum autoclave, medical waste shall be subjected to a minimum of one pre-vacuum pulse to purge the autoclave of all air. The waste shall be subjected to the following:
- a temperature of not less than 121 C° and pressure of 15 psi per an autoclave residence time of not less than 45 minutes; or
- a temperature of not less than 135 C° and a pressure of 31 psi for an autoclave residence time of not less than 30 minutes;
- Medical waste shall not be considered properly treated unless the time, temperature and pressure indicators indicate that the required time, temperature and pressure were reached during the autoclave process. If for any reasons, time temperature or pressure indicator indicates that the required temperature, pressure or residence time was not reached, the entire load of medical waste must be autoclaved again until the proper temperature, pressure and residence time were achieved.
- Recording of operational parameters Each autoclave shall have graphic or computer recording devices which will automatically and continuously monitor and record dates, time of day, load identification number and operating parameters throughout the entire length of the autoclave cycle.
- Validation test Spore testing: The autoclave should completely and consistently kill the approved biological indicator at the maximum design capacity of each autoclave unit. Biological indicator for autoclave shall be Bacillus stearothermophilus spores using vials or spore Strips; with at least 1X104 spores per millilitre. Under no circumstances will an autoclave have minimum operating parameters less than a residence time of 30 minutes, regardless of temperature and pressure, a temperature less than 121 C° or a pressure less than 15 psi.
- Routine Test A chemical indicator strip/tape that changes colour when a certain temperature is reached can be used to verify that a specific temperature has been achieved. It may be necessary to use more than one strip over the waste package at different location to ensure that the inner content of the package has been adequately autoclaved
III.STANDARDS FOR LIQUID WASTE :
The effluent generated from the hospital should conform to the following limits
PARAMETERS
- PH
- Susponded solids
- Oil and grease
- BOD
- COD
- Bio-assay test
PERMISSIBLE LIMITS
- 6.3-9.0
- 100 mg/l
- 10 mg/l
- 30 mg/l
- 250 mg/l
- 90% survival of fish after 96 hours in 100% effluent.
These limits are applicable to those, hospitals which are either connected with sewers without terminal sewage treatment plant or not connected to public sewers. For discharge into public sewers with terminal facilities, the general standards as notified under the Environment (Protection) Act, 1986 shall be applicable.
IV.STANDARDS FOR MICROWAVING :
- Microwave treatment shall not be used for cytotoxic, hazardous or radioactive wastes, contaminated animal car casses, body parts and large metal items.
- The microwave system shall comply with the efficacy test/routine tests and a performance guarantee may be provided by the supplier before operation of the limit.
- The microwave should completely and consistently kill the bacteria and other pathogenic organisms that is ensured by approved biological indicator at the maximum design capacity of each microwave unit. Biological indicators for microwave shall be Bacillus Subtilis spores using vials or spore strips with at least 1 x 101 spores per milliliter.
V.STANDARDS FOR DEEP BURIAL:
- A pit or trench should he dug about 2 meters deep. It should be half filled with waste, then covered with lime within 50 cm of the surface, before filling the rest of the pit with soil.
- It must be ensured that animals do not have any access to burial sites. Covers of galvanised iron/wire meshes may be used.
- On each occasion, when wastes are added to the pit, a layer of 10 em of soil shall be added to cover the wastes.
- Burial must be performed under close and dedicated supervision.
- The deep burial site should be relatively impermeable and no shallow well should be close to the site.
- The pits should be distant from habitation, and sited so as to ensure that no contamination occurs of any surface water or ground water. The area should not be prone to flooding or erosion.
- The location of the deep burial site will be authorised by the prescribed authority.
- The institution shall maintain a record of all pits for deep burial.