You are here :
Home Chinakuri Colliery on 19.2.1958
|
Last Updated:: 10/02/2017
Chinakuri Colliery on 19.2.1958
Chinakuri Colliery
Date of the Accident |
- 19.2.1958 |
Number of persons killed |
- 183 |
Owner |
- Bengal Coal Co. |
Place |
- Raniganj Coalfield |
The Chinakuri Colliery was a combined mine consisting of the workings of Nos. 1 and 2 pits colliery and of No.3 pit colliery working the Disergarh seam. The Disergarh seam was known to produce inflammable gas and its average make in the workings of Nos. 1 and 2 pits was 8.5 m3/min.
The explosion took place in the workings of Nos. l and 2 pits on 19th February, 1958 at about 9.45 p.m. On the surface, first a loud hissing sound was heard, and then there was a loud report. A tongue of fire about 1m long was seen in the fan evasee. This flame was partly bluish and partly yellowish in colour and lasted only for a few seconds. Men underground in No.3 pit were withdrawn by 10.30 p.m.
Cages in No.1 pit could not be wound as the lower cage got jammed. The shaft covers of No.2 pit (up-cast) which had been blown upwards were secured and the cages in this shaft were wound a number of times to ensure that the shaft was free from obstructions and that it was safe to send down a team.
The first rescue team was sent down at 11.50 p.m. and returned within 10 minutes as had been agreed upon. They brought with them one survivor. The same rescue team went down again at 12.15 a.m. The derangement of shaft signals made it necessary to arrange for the cages to be wound every 10 minutes. By about 4 a.m. there were altogether 27 teams of 5 men each available for rescue work. Altogether 20 men were rescued that night and out of them 4 died later.
With the return of the third rescue team to the surface there was a discussion and it was considered by one and all that the possibility of life underground under the conditions reported was nil. In view of the open flames seen underground by the last team and the inevitability of further explosions of methane which was building up in the galleries as a result of the derangement of the ventilation system with the destruction of doors and stoppings, it would be hazardous to risk any further rescue parties underground. Accordingly, at about 4.30 a.m. it was finally decided that no further rescue team should be sent underground. It was further decided to stop the fan and it was stopped at 4.50 a.m. Then light seals were built at the mouths of Nos.1 and 3 pits, the sand stowing pit and the sand stowing drift. The mouth of No.2 pit was left open. These seals were completed by 9.30 a.m. on 20th February. At about 11 a.m. traces of smoke were seen coming out of No.2 pit and an attempt was made to tighten up the seals at No.1 pit to prevent the ingress of air. But at 11.30 a.m., there occurred a rapid succession of two explosions which blew off the seal at the mouth of No.1 pit and the stopping at the mouth of the sand stowing drift. The explosions were followed by the emission of large quantities of black smoke from No.2 pit. No.1 pit still continued to downcast and it was apparent from the volume of smoke coming out of No.2 pit that there was a substantial fire in the underground workings, it was considered unsafe to engage persons for building up seals at the top of either of the shafts. It was then decided to put out the fire by flooding the mine with water and in the mean time to seal the mouth of No.1 pit by using a scraper conveyor to dump down the shaft bricks, clays, mattings, etc.
The first pontoon-mounted pump with a capacity of 4550 m3/hr started pumping water into the sand stowing drift at 12.30 p.m. on 20th February, 1958. On the same day at about 5 p.m. the conveyor had started delivering sand etc. into No.1 pit and the mouth of the sand stowing drift was re-sealed by 5.30 p.m. By 3 p.m. on 22nd February, the introduction of sand etc. into No.1 pit was completed. At 2.30 p.m. on the 24th February when it was found on a rough measurement of the water in No.2 pit that the water had risen above the necessary level, the pumping of water into the sand stowing drift was stopped.
Cause of the explosion
There was a large outburst of gas from the splinter seam immediately beneath the Disergarh seam. This splinter seam was known for its inherent gassy nature having confined gas under pressure. The intervening strata had become so thin that it was no longer able to repress the upward progress of the gas and consequently the floor was lifted, liberating a large volume of gas which caused the explosion.
This view is supported by the following facts:
- Bluish methane flame streaked with yellow in the fan evasee immediately after the explosion.
- About 3 hours after the explosion, samples of gas taken on the surface showed 2.5% CH4 indicating that inside the shafts concentration of CH4 was much higher.
- Impossibility of such a build up of gas in the mine from its natural make without its being detected.
- The large majority of the dead bodies was found at or near the working faces suggesting that they were overpowered by such an unexpected danger that they could not make the least attempt to save themselves.
As regards the source of ignition, the Court of Inquiry concluded that a flame shooting out from diesel loco inlet might have ignited the explosive mixture of methane and air. While on the exhaust, a flame-trap was provided, there was none on the inlet side. The absence of such flame traps on the locomotives renders them potential sources of ignition when they are, operated in an explosive atmosphere.
The outburst of methane must have been accompanied by certain quantity of small coal from the splinter seam and therefore coal dust must have taken part from an early stage and assumed somewhat important role as the explosion reached the downcast area, that is, the region of fresh air.
The Court of Inquiry appointed to inquire into the causes of, and circumstances attending the explosion made the following recommendations:
- In all gassy mines a continuously automatic recording water gauge of approved type should be fitted to the main fan at the surface. Such a recording gauge, if there was one in this mine, would have shown at once that’ there was an outburst of gas, and removed doubts and arguments and saved much time in the inquiry. It will also show to the management whether the fan is operating normally and whether there are any unusual conditions in the mine.
- No apparatus should be accepted in India as certified flame-proof without report by the engineer or representative supplying the equipment that he has personally seen that it is properly assembled and in safe condition. It should be made illegal to attach the official flame-proof label to this equipment unless the whole equipment is rendered flame-proof with all flame-traps and similar devices affixed and in order.
- The matter of appointment of one or more mechanical engineers to the staff of the Mines Inspectorate is crucially urgent as mine mechanization is now proceeding apace. With the growth of mining in India, the Inspectorate should be generally strengthened particularly with specialists in ventilation, strata-stresses, explosions and the like.
- The Central Mining Research Station should be asked to undertake more extensive research work in suppression of explosions and other mining hazards.
- Rescue teams did not take sufficient air samples from the underground workings which they visited. There should be a rule compelling the taking of air samples by rescue teams. Sampling equipment should be devised so that it should form part and parcel of the rescue equipment.
- There should be one or two portable Haldane gas analysis apparatus, or the like, maintained in working order at every rescue station and one or two members of the rescue station staff should be trained in the correct operation of the apparatus.
- Enough teams were not sent underground so as to render simultaneous exploration of the western and the eastern districts possible and that the first two teams did not go at all to the eastern side and make an attempt to rescue survivors from that region. Although there is nothing in the Coal Mines Rescue Rules, 1939, it is a recognized practice that only one team at a time is sent underground as otherwise confusion may arise. This practice regarding sending forward only one rescue team after an extensive mine accident should be reconsidered.
- In gassy mines, especially where the seam appears to have less than its normal thickness, 3 m deep boreholes shall be put down at intervals of 90 m to explore whether there is an approaching seam or whether there is excessive liberation of gas.
- Mine dust samples should be taken over a length of roadway not exceeding 100 m and the mine should be divided into convenient zones to be approved by RIM. The dust of each zone shall be tested at least once a month.
News Clipping:
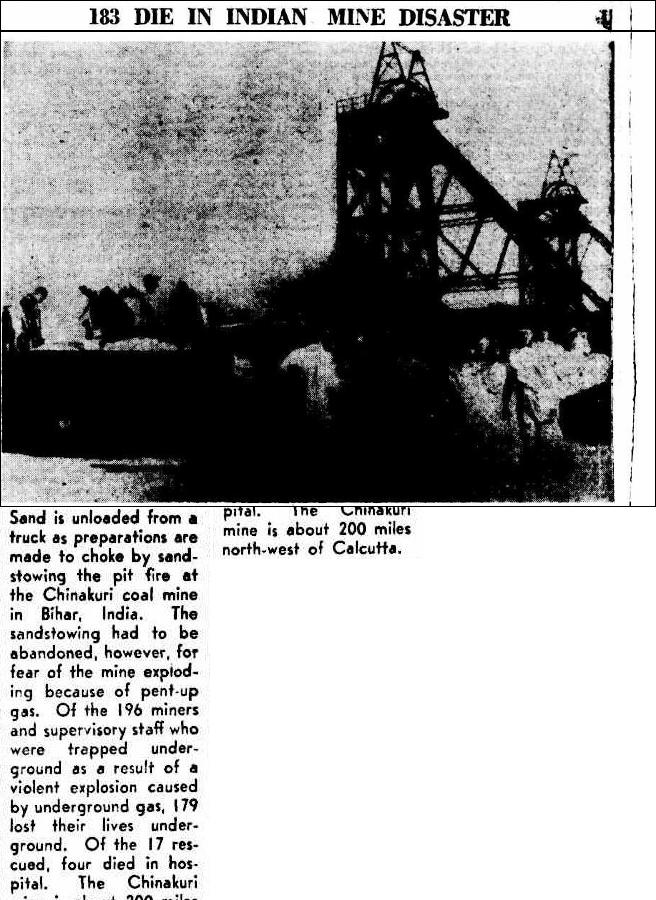
(Source: http://trove.nla.gov.au/newspaper/article/91244589#)